greyhound bet tv
mitzvahceremonies.com:2025/3/1 23:00:00
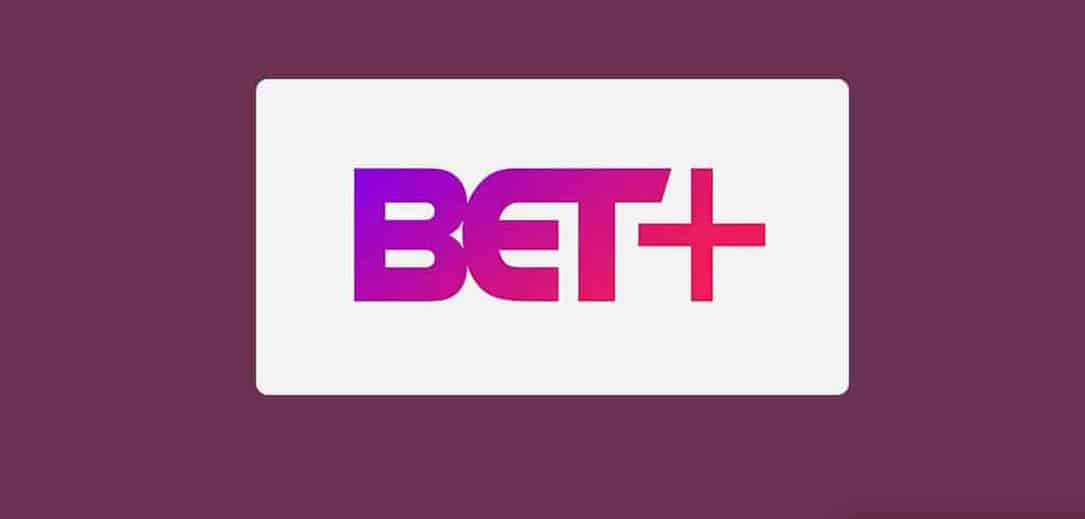
greyhound bet tv
As luzes se apagaram no triunfo histórico da Liga dos Campeões do Barcelona, surgiu a pergunta: "E agora?"
📉 Após a vitória histórica do Barcelona na Liga dos Campeões greyhound bet tv maio, a maior pergunta greyhound bet tv minha mente foi 📉 "O que agora?". Por primeira vez greyhound bet tv dois anos, estávamos enfrentando uma lacuna de três meses sem futebol. Sim, os 📉 Jogos Olímpicos estavam à vista, mas sem a participação da Seleção Britânica, as oportunidades eram limitadas.
📉 Nossos olhos imediatamente se voltaram para os EUA. Não houve surpresa entre amigos e familiares quando anunciamos que uma 📉 folga de motorista era a única verdadeira solução para o problema de ter tempo livre. A NWSL tem sido uma 📉 fonte de interesse por anos. Uma visita ao Angel City greyhound bet tv nosso retorno da Copa do Mundo do ano passado 📉 nos deu um gosto da liga e nos deixou com o desejo de aprender mais.
📉 A NWSL cresce enquanto a WSL se expande
Enquanto a WSL cresce imensamente, o futebol 📉 feminino também cresce nos EUA. Quando eu era jovem, muitas jogadoras se dirigiam para o exterior, primeiro para o sistema 📉 de faculdades renomado antes de entrar na "Women's Professional Soccer", a liga profissional então que foi dissolvida greyhound bet tv 2012. Desde 📉 então, a NWSL nasceu e, apesar de enfrentar algumas dificuldades, a liga está florescendo. O dinheiro envolvido é cegador. Seja 📉 a Bay FC quebrando o recorde mundial de transferências duas vezes, Bob Iger e Willow Bay adquirindo uma participação controladora 📉 na Angel City por USR$ 250 milhões (£ 191 milhões) ou o contrato de transmissão de USR$ 60 milhões por 📉 temporada, não há dúvidas de que está desfrutando de um crescente sucesso.
Explorando a NWSL 📉 de uma perspectiva de fã
Com a tomada da WPL das Ligas Profissionais Femininas da 📉 WSL e da Championship este verão, parecia a oportunidade perfeita para explorar tudo o que a NWSL tem a oferecer 📉 do ponto de vista de um fã. Embarcamos greyhound bet tv uma turnê de cinco semanas, visitamos seis estádios, assistimos a 10 📉 dos 12 times, desfrutamos de nossa primeira experiência de tailgating e conversamos com vários fãs. O que aprendi com nossas 📉 experiências? O que gostaria de ver implementado greyhound bet tv casa? Houve alguma surpresa?
O que é 📉 imediatamente evidente é que os EUA se saem bem greyhound bet tv hospedar esportes. Desde o futebol ao beisebol ao basquete, as 📉 organizações priorizam o evento como um todo e os espectadores que entram greyhound bet tv seus portões. Mais de um milhão de 📉 fãs compareceram a jogos da NWSL até julho e estava claro por que. Alguns fazem isso melhor do que outros, 📉 mas no geral, a experiência do fã é incomparável a qualquer lugar onde eu já estive na Europa.
📉 Mercadoria acessível e conexões comunitárias
Seu sucesso vem de fornecer múltiplos ganchos 📉 para convidar as pessoas a entrar. Um desses é o amplo leque de mercadorias e a acessibilidade a ele. Os 📉 fãs de esportes gostam de gastar dinheiro, mas quando olho para a WSL, historicamente foi difícil mesmo conseguir uma camisa 📉 com uma jogadora feminina no verso. Min
Betnacional Aplicativo Android
0 5 apostas
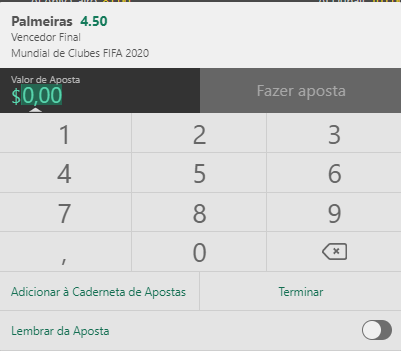
Process that helps an equipment operator avoid mistakes
Poka-yoke (ポカヨケ, [poka joke]) is
a Japanese term that means "mistake-proofing" or "error 3️⃣ prevention". It is also
sometimes referred to as a forcing function or a behavior-shaping constraint.
A
poka-yoke is any mechanism in 3️⃣ a process that helps an equipment operator avoid (yokeru)
mistakes (poka) and defects by preventing, correcting, or drawing attention to 3️⃣ human
errors as they occur.[1] The concept was formalized, and the term adopted, by Shigeo
Shingo as part of the 3️⃣ Toyota Production System.[2][3]
Etymology [ edit ]
Poka-yoke was
originally baka-yoke, but as this means "fool-proofing" (or "idiot-proofing") the name
was changed 3️⃣ to the milder poka-yoke.[4] Poka-yoke is derived from poka o yokeru
(ポカを避ける), a term in shogi that means avoiding an 3️⃣ unthinkably bad move.
Usage and
examples [ edit ]
More broadly, the term can refer to any behavior-shaping constraint
designed into a 3️⃣ process to prevent incorrect operation by the user.
A simple poka-yoke
example is demonstrated when a driver of the car equipped 3️⃣ with a manual gearbox must
press on the clutch pedal (a process step, therefore a poka-yoke) prior to starting an
3️⃣ automobile.[5] The interlock serves to prevent unintended movement of the car. Another
example of poka-yoke would be the car equipped 3️⃣ with an automatic transmission, which
has a switch that requires the car to be in "Park" or "Neutral" before the 3️⃣ car can be
started (some automatic transmissions require the brake pedal to be depressed as well).
These serve as behavior-shaping 3️⃣ constraints as the action of "car in Park (or Neutral)"
or "foot depressing the clutch/brake pedal" must be performed before 3️⃣ the car is allowed
to start. The requirement of a depressed brake pedal to shift most of the cars with 3️⃣ an
automatic transmission from "Park" to any other gear is yet another example of a
poka-yoke application. Over time, the 3️⃣ driver's behavior is conformed with the
requirements by repetition and habit.
When automobiles first started shipping with
on-board GPS systems, it 3️⃣ was not uncommon to use a forcing function which prevented the
user from interacting with the GPS (such as entering 3️⃣ in a destination) while the car
was in motion. This ensures that the driver's attention is not distracted by the 3️⃣ GPS.
However, many drivers found this feature irksome, and the forcing function has largely
been abandoned. This reinforces the idea 3️⃣ that forcing functions are not always the best
approach to shaping behavior.
The microwave oven provides another example of a forcing
3️⃣ function.[6] In all modern microwave ovens, it is impossible to start the microwave
while the door is still open. Likewise, 3️⃣ the microwave will shut off automatically if
the door is opened by the user. By forcing the user to close 3️⃣ the microwave door while
it is in use, it becomes impossible for the user to err by leaving the door 3️⃣ open.
Forcing functions are very effective in safety critical situations such as this, but
can cause confusion in more complex 3️⃣ systems that do not inform the user of the error
that has been made.
These forcing functions are being used in 3️⃣ the service industry as
well. Call centers concerned with credit card fraud and friendly fraud are using
agent-assisted automation to 3️⃣ prevent the agent from seeing or hearing the credit card
information so that it cannot be stolen. The customer punches 3️⃣ the information into
their phone keypad, the tones are masked to the agent and are not visible in the
customer 3️⃣ relationship management software.[7]
History [ edit ]
The term poka-yoke was
applied by Shigeo Shingo in the 1960s to industrial processes designed 3️⃣ to prevent human
errors.[1] Shingo redesigned a process in which factory workers, while assembling a
small switch, would often forget 3️⃣ to insert the required spring under one of the switch
buttons. In the redesigned process, the worker would perform the 3️⃣ task in two steps,
first preparing the two required springs and placing them in a placeholder, then
inserting the springs 3️⃣ from the placeholder into the switch. When a spring remained in
the placeholder, the workers knew that they had forgotten 3️⃣ to insert it and could
correct the mistake effortlessly.[8]
Shingo distinguished between the concepts of
inevitable human mistakes and defects in 3️⃣ the production. Defects occur when the
mistakes are allowed to reach the customer. The aim of poka-yoke is to design 3️⃣ the
process so that mistakes can be detected and corrected immediately, eliminating defects
at the source.
Implementation in manufacturing [ edit 3️⃣ ]
Poka-yoke can be implemented at
any step of a manufacturing process where something can go wrong or an error can 3️⃣ be
made.[9] For example, a fixture that holds pieces for processing might be modified to
only allow pieces to be 3️⃣ held in the correct orientation,[10] or a digital counter might
track the number of spot welds on each piece to 3️⃣ ensure that the worker executes the
correct number of welds.[10]
Shingo recognized three types of poka-yoke for detecting
and preventing errors 3️⃣ in a mass production system:[2][9]
The contact method identifies
product defects by testing the product's shape, size, color, or other physical
3️⃣ attributes. The fixed-value (or constant number) method alerts the operator if a
certain number of movements are not made. The 3️⃣ motion-step (or sequence) method
determines whether the prescribed steps of the process have been followed.
Either the
operator is alerted when 3️⃣ a mistake is about to be made, or the poka-yoke device
actually prevents the mistake from being made. In Shingo's 3️⃣ lexicon, the former
implementation would be called a warning poka-yoke, while the latter would be referred
to as a control 3️⃣ poka-yoke.[2]
Shingo argued that errors are inevitable in any
manufacturing process, but that if appropriate poka-yokes are implemented, then
mistakes can 3️⃣ be caught quickly and prevented from resulting in defects. By eliminating
defects at the source, the cost of mistakes within 3️⃣ a company is reduced.[citation
needed]
Benefits of poka-yoke implementation [ edit ]
A typical feature of poka-yoke
solutions is that they don't 3️⃣ let an error in a process happen. Other advantages
include:[11]
Less time spent on training workers;
Elimination of many operations
related to 3️⃣ quality control;
Unburdening of operators from repetitive
operations;
Promotion of the work improvement-oriented approach and actions;
A reduced
number of rejects;
Immediate action when 3️⃣ a problem occurs;
100% built-in quality
control;
Preventing bad products from reaching customers;
Detecting mistakes as they
occur;
Eliminating defects before they occur.
See also 3️⃣ [ edit ]
References [ edit ]
artigos relacionados
2025/3/1 23:00:00