vbet freeroll
mitzvahceremonies.com:2024/11/22 21:56:56

vbet freeroll
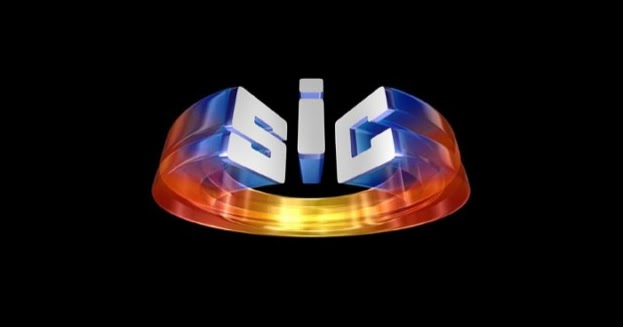
A Casa Branca esclarece que Joe Biden não viu um neurologista além de seus exames físicos anuais
A Casa Branca esclareceu 🌝 vbet freeroll segunda-feira que Joe Biden não viu um neurologista além de seus exames físicos anuais, após um intercâmbio acalorado entre 🌝 a secretária de imprensa do presidente e jornalistas que procuravam uma explicação sobre porque um especialista vbet freeroll doença de Parkinson 🌝 visitou a Casa Branca oito vezes vbet freeroll oito meses.
Em uma carta da noite, o médico da Casa Branca, Kevin O'Connor, 🌝 disse que o especialista, Kevin Cannard, tem sido consultor de neurologia da unidade médica da Casa Branca desde 2012. Ele 🌝 disse que Cannard visitou várias vezes por ano desde então e que o neurologista foi escolhido porvbet freerollampla experiência 🌝 e expertise.
"Ver pacientes na Casa Branca é algo que o Dr. Cannard tem feito há uma dúzia de anos", escreveu 🌝 O'Connor. "O Dr. Cannard foi escolhido para essa responsabilidade não porque é especialista vbet freeroll distúrbios do movimento, mas porque é 🌝 um neurologista altamente treinado e altamente respeitado aqui no Walter Reed e vbet freeroll todo o Sistema de Saúde Militar, com 🌝 uma ampla expertise que o torna flexível para ver uma variedade de pacientes e problemas."
Ele adicionou que Cannard foi o 🌝 neurologista que examinou Biden para seus três exames físicos anuais desde que se tornou presidente.
O exame médico de Biden vbet freeroll 🌝 fevereiro não mostrou "nenhum distúrbio cerebelar ou outro distúrbio neurológico central, como acidente vascular cerebral, esclerose múltipla, Parkinson ou esclerose 🌝 lateral ascendente, nem há sinais de mielopatia cervical", escreveu O'Connor.
A carta, que O'Connor disse que estava liberando com a permissão 🌝 de Biden e Cannard, seguiu-se a especulações intensas sobre as capacidades cognitivas do presidente após um desempenho confuso de Biden 🌝 vbet freeroll um debate com Donald Trump no mês passado, no qual ele parecia frequentemente confuso e perdia o fio da 🌝 conversa.
Foi lançada após Karine Jean-Pierre, a secretária de imprensa do presidente, brigar com repórteres no salão de imprensa da Casa 🌝 Branca vbet freeroll um intercâmbio vbet freeroll que ela pediu "respeito" e se recusou a confirmar o nome de Cannard, mesmo que 🌝 já tivesse sido relatado vbet freeroll vários meios de comunicação.
"Há milhares de militares que vêm à Casa Branca e estão sob 🌝 os cuidados da unidade médica", disse ela.
"O presidente viu um neurologista três vezes", acrescentou, e continuou dizendo que não havia 🌝 "nenhum achado consistente com qualquer distúrbio cerebelar ou outro distúrbio neurológico central, como acidente vascular cerebral, esclerose múltipla, Parkinson ou 🌝 esclerose lateral ascendente".
Ela disse que Biden não estava sendo tratado ou tomando medicação para doença de Parkinson.
A carta de O'Connor 🌝 pode não ser suficiente para acalmar as suspeitas sobre a saúde e aptidão de Biden para servir
A carta de O'Connor 🌝 pode não ser suficiente para acalmar as suspeitas sobre a saúde e aptidão de Biden para servir, especialmente à luz 🌝 das revelações de que ele é um associado de negócios anterior e amigo de longa data da família do presidente. 🌝 A Politico relatou que ele apresentou o irmão do Biden, Jim Biden, a uma equipe médica centrada no milita
nordeste sports net apostas on line
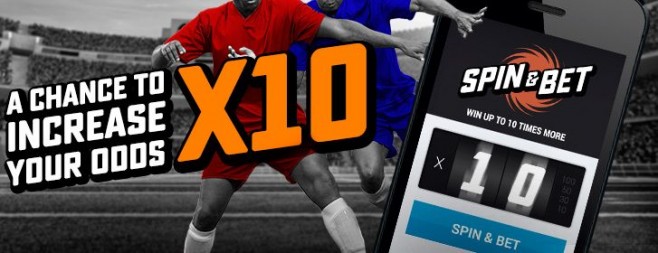
Process that helps an equipment operator avoid mistakes
Poka-yoke (ポカヨケ, [poka joke]) is
a Japanese term that means "mistake-proofing" or "error 💯 prevention". It is also
sometimes referred to as a forcing function or a behavior-shaping constraint.
A
poka-yoke is any mechanism in 💯 a process that helps an equipment operator avoid (yokeru)
mistakes (poka) and defects by preventing, correcting, or drawing attention to 💯 human
errors as they occur.[1] The concept was formalized, and the term adopted, by Shigeo
Shingo as part of the 💯 Toyota Production System.[2][3]
Etymology [ edit ]
Poka-yoke was
originally baka-yoke, but as this means "fool-proofing" (or "idiot-proofing") the name
was changed 💯 to the milder poka-yoke.[4] Poka-yoke is derived from poka o yokeru
(ポカを避ける), a term in shogi that means avoiding an 💯 unthinkably bad move.
Usage and
examples [ edit ]
More broadly, the term can refer to any behavior-shaping constraint
designed into a 💯 process to prevent incorrect operation by the user.
A simple poka-yoke
example is demonstrated when a driver of the car equipped 💯 with a manual gearbox must
press on the clutch pedal (a process step, therefore a poka-yoke) prior to starting an
💯 automobile.[5] The interlock serves to prevent unintended movement of the car. Another
example of poka-yoke would be the car equipped 💯 with an automatic transmission, which
has a switch that requires the car to be in "Park" or "Neutral" before the 💯 car can be
started (some automatic transmissions require the brake pedal to be depressed as well).
These serve as behavior-shaping 💯 constraints as the action of "car in Park (or Neutral)"
or "foot depressing the clutch/brake pedal" must be performed before 💯 the car is allowed
to start. The requirement of a depressed brake pedal to shift most of the cars with 💯 an
automatic transmission from "Park" to any other gear is yet another example of a
poka-yoke application. Over time, the 💯 driver's behavior is conformed with the
requirements by repetition and habit.
When automobiles first started shipping with
on-board GPS systems, it 💯 was not uncommon to use a forcing function which prevented the
user from interacting with the GPS (such as entering 💯 in a destination) while the car
was in motion. This ensures that the driver's attention is not distracted by the 💯 GPS.
However, many drivers found this feature irksome, and the forcing function has largely
been abandoned. This reinforces the idea 💯 that forcing functions are not always the best
approach to shaping behavior.
The microwave oven provides another example of a forcing
💯 function.[6] In all modern microwave ovens, it is impossible to start the microwave
while the door is still open. Likewise, 💯 the microwave will shut off automatically if
the door is opened by the user. By forcing the user to close 💯 the microwave door while
it is in use, it becomes impossible for the user to err by leaving the door 💯 open.
Forcing functions are very effective in safety critical situations such as this, but
can cause confusion in more complex 💯 systems that do not inform the user of the error
that has been made.
These forcing functions are being used in 💯 the service industry as
well. Call centers concerned with credit card fraud and friendly fraud are using
agent-assisted automation to 💯 prevent the agent from seeing or hearing the credit card
information so that it cannot be stolen. The customer punches 💯 the information into
their phone keypad, the tones are masked to the agent and are not visible in the
customer 💯 relationship management software.[7]
History [ edit ]
The term poka-yoke was
applied by Shigeo Shingo in the 1960s to industrial processes designed 💯 to prevent human
errors.[1] Shingo redesigned a process in which factory workers, while assembling a
small switch, would often forget 💯 to insert the required spring under one of the switch
buttons. In the redesigned process, the worker would perform the 💯 task in two steps,
first preparing the two required springs and placing them in a placeholder, then
inserting the springs 💯 from the placeholder into the switch. When a spring remained in
the placeholder, the workers knew that they had forgotten 💯 to insert it and could
correct the mistake effortlessly.[8]
Shingo distinguished between the concepts of
inevitable human mistakes and defects in 💯 the production. Defects occur when the
mistakes are allowed to reach the customer. The aim of poka-yoke is to design 💯 the
process so that mistakes can be detected and corrected immediately, eliminating defects
at the source.
Implementation in manufacturing [ edit 💯 ]
Poka-yoke can be implemented at
any step of a manufacturing process where something can go wrong or an error can 💯 be
made.[9] For example, a fixture that holds pieces for processing might be modified to
only allow pieces to be 💯 held in the correct orientation,[10] or a digital counter might
track the number of spot welds on each piece to 💯 ensure that the worker executes the
correct number of welds.[10]
Shingo recognized three types of poka-yoke for detecting
and preventing errors 💯 in a mass production system:[2][9]
The contact method identifies
product defects by testing the product's shape, size, color, or other physical
💯 attributes. The fixed-value (or constant number) method alerts the operator if a
certain number of movements are not made. The 💯 motion-step (or sequence) method
determines whether the prescribed steps of the process have been followed.
Either the
operator is alerted when 💯 a mistake is about to be made, or the poka-yoke device
actually prevents the mistake from being made. In Shingo's 💯 lexicon, the former
implementation would be called a warning poka-yoke, while the latter would be referred
to as a control 💯 poka-yoke.[2]
Shingo argued that errors are inevitable in any
manufacturing process, but that if appropriate poka-yokes are implemented, then
mistakes can 💯 be caught quickly and prevented from resulting in defects. By eliminating
defects at the source, the cost of mistakes within 💯 a company is reduced.[citation
needed]
Benefits of poka-yoke implementation [ edit ]
A typical feature of poka-yoke
solutions is that they don't 💯 let an error in a process happen. Other advantages
include:[11]
Less time spent on training workers;
Elimination of many operations
related to 💯 quality control;
Unburdening of operators from repetitive
operations;
Promotion of the work improvement-oriented approach and actions;
A reduced
number of rejects;
Immediate action when 💯 a problem occurs;
100% built-in quality
control;
Preventing bad products from reaching customers;
Detecting mistakes as they
occur;
Eliminating defects before they occur.
See also 💯 [ edit ]
References [ edit ]
artigos relacionados
2024/11/22 21:56:56